Process Improvement: Key Benefits for Your Organization
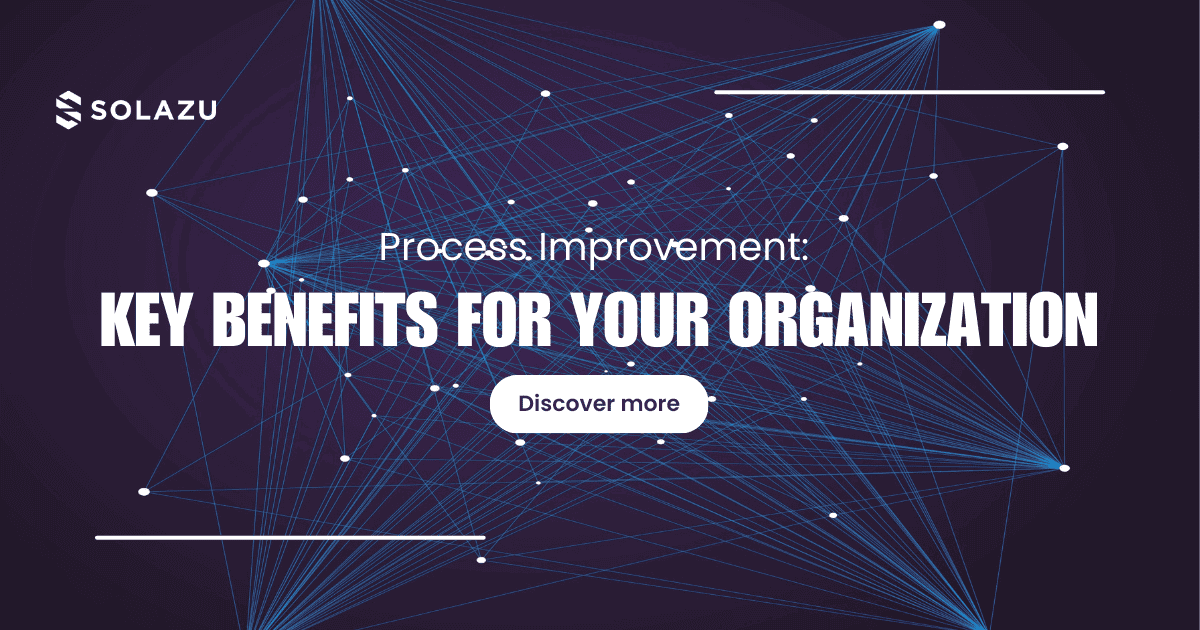
In today’s fast-paced business world, inefficiencies in workflows can lead to wasted resources, unnecessary costs, and lost opportunities. While many organizations recognize the need for change, they often struggle with where to begin.
At Solazu, we believe process improvement isn’t just about fixing issues—it’s about unlocking potential. By streamlining operations, reducing redundancies, and fostering a culture of continuous improvement, businesses can transform disorganization into clarity and drive meaningful growth.
If you’re ready to elevate your organization’s efficiency, innovation, and customer satisfaction, this guide will help you:
- Understand process improvement.
- Explore its key benefits.
- Learn how to identify bottlenecks
- Learn how to design efficient solutions.
- Explore actionable strategies for implementation.
- Measure success to ensure long-term results.
Let’s dive in!
Understanding Process Improvement
Process improvement refers to systematically analyzing, refining, and optimizing business workflows to improve efficiency, productivity, and outcomes. At its heart, it’s about:
- Identifying inefficiencies that hinder performance.
- Implementing solutions to streamline operations.
- Fostering continuous innovation to stay agile in changing markets.
When done right, process improvement creates an environment of operational excellence, where every task adds value, every resource is optimized, and every team member is empowered to succeed.
Benefits of Process Improvement
Implementing process improvement strategies can be transformative. Here’s how it benefits organizations:
1. Cost Reduction
Inefficient processes waste time, energy, and resources. Process improvement identifies and eliminates redundancies, minimizes errors, and optimizes resource allocation, resulting in significant cost savings.
For example, lean methodologies have helped organizations reduce waste by up to 30%, enabling smarter investments in innovation and growth.
2. Improved Productivity
Streamlined processes allow teams to focus on high-value tasks rather than being bogged down by repetitive or unnecessary steps. When workflows are clear and efficient:
- Employees work with less frustration.
- Tasks are completed faster and with greater accuracy.
- Teams collaborate seamlessly across departments.
Example: A manufacturing company improved production cycles by 40% after redesigning workflows and removing bottlenecks.
3. Enhanced Customer Satisfaction
Happy customers are the result of faster, higher-quality service. Process improvements lead to:
- Shorter delivery times.
- Fewer errors in products/services.
- Consistent, reliable experiences.
By meeting or exceeding customer expectations, businesses build loyalty and a competitive edge in the market.
4. Employee Engagement
Clear processes empower employees to work efficiently and feel confident in their roles. When teams are involved in improvement initiatives, they feel heard, valued, and motivated to contribute ideas for further optimization.
Identifying Workflow Bottlenecks
Workflow bottlenecks are the roadblocks that hinder progress, slow operations, and frustrate employees. Common bottlenecks include:
- Repetitive manual tasks.
- Poor communication between teams.
- Outdated technology or systems.
- Inefficient approval processes.
Steps to Identify Bottlenecks:
- Map Current Workflows: Visualize each step of the process to identify where delays occur.
- Gather Team Feedback: Employees working within the process often know its weak points best.
- Analyze Data: Use tools to track metrics like turnaround times, error rates, and workload distribution.
- Prioritize Issues: Focus on bottlenecks with the greatest impact on time, cost, or customer satisfaction.
Designing Efficient Solutions
Creating efficient processes begins with identifying gaps and designing targeted solutions that align with your business goals. Here’s how to build an optimized framework:
1. Map Existing Workflows
Start by visualizing your current processes. Use tools like Lucidchart or Visio to create process maps, which clearly outline each step of your workflows. This helps pinpoint where bottlenecks occur, redundancies exist, or manual tasks slow operations down.
Example: A company discovered that approval delays in purchase orders were caused by an unnecessary 3-step sign-off process. By mapping the workflow, they reduced approvals to a single step, saving hours every week.
2. Prioritize Improvements
Not every issue requires immediate attention. Focus on changes that have the greatest impact on cost savings, productivity, or customer experience. Prioritization ensures resources are used effectively.
Quick Wins: Simple changes like automating repetitive tasks.
Long-Term Goals: Larger initiatives like overhauling outdated systems.
3. Adopt Automation and Technology
Automation is a game-changer for process improvement. Tools like UiPath for robotic process automation (RPA) or Zapier for automating tasks help streamline workflows, reduce errors, and free up valuable time.
Benefits of Automation:
• Tasks are completed faster and with greater accuracy.
• Employees focus on high-value, strategic work.
• Errors from manual data entry are significantly reduced.
4. Involve Teams in Solution Design
The people who work within your processes every day know them best. Engage cross-functional teams to design solutions that are both practical and impactful.
• Feedback Loops: Encourage team suggestions during brainstorming sessions.
• Pilot Programs: Test proposed solutions on a smaller scale before full implementation.
5. Focus on Scalability and Flexibility
Efficient solutions should not only solve today’s problems but also scale as your organization grows. Modular designs allow you to add or adjust processes without starting over.
• Example: A logistics firm integrated a flexible scheduling tool that scaled with increased delivery volumes during peak seasons.
Strategies for Effective Process Improvement
Once efficient solutions are designed, implementing them strategically ensures long-term success. Here’s how:
1. Set Clear, Measurable Objectives
Start by defining specific, achievable goals tied to process improvement. Clear objectives act as a roadmap, guiding teams toward measurable success.
Example Goals:
• Reduce processing time by 30%.
• Increase on-time deliveries to 98%.
• Eliminate 50% of manual data entry tasks.
2. Engage Stakeholders and Teams
Change is most successful when everyone is aligned. From leadership to frontline employees, ensure that all stakeholders understand why improvements are necessary and how they contribute to success.
Steps to Build Buy-In:
• Share the vision and benefits of process changes.
• Host workshops or training sessions to address concerns.
• Celebrate small wins to build momentum and trust.
3. Incorporate Lean Methodologies
Lean principles focus on eliminating waste and increasing value. By identifying non-essential steps, organizations improve workflows and streamline operations.
Key Lean Techniques:
• Value Stream Mapping: Analyze the flow of processes to identify inefficiencies.
• 5S Methodology: Sort, set, shine, standardize, and sustain for better workspace organization.
4. Use Data to Drive Decisions
Process improvement isn’t guesswork—it’s driven by data. Track metrics like cycle time, resource usage, and error rates to measure performance before and after changes.
Tools:
• Real-time analytics platforms like Tableau and Power BI provide actionable insights.
5. Monitor, Evaluate, and Refine
Process improvement is an ongoing effort. Regularly assess results, gather feedback, and refine solutions to adapt to changing needs.
Metrics to Track:
• Cost savings achieved.
• Productivity improvements.
• Employee satisfaction.
• Customer satisfaction scores.
Conclusion
In an era where agility and efficiency are critical for success, process improvement offers businesses the tools to adapt, thrive, and innovate. By designing efficient solutions, implementing strategies strategically, and measuring success, organizations can reduce costs, improve productivity, and deliver exceptional customer experiences.
At Solazu, we specialize in helping businesses identify bottlenecks, design optimized workflows, and drive continuous improvement.
Are you ready to transform inefficiencies into opportunities? Contact us today to start your process improvement journey and unlock lasting success.
次のステップへよりスマートなソリューションへ
貴社の業務効率化、コスト削減、持続的な成長を実現する戦略をご提案します。今すぐ無料相談を予約し、Solazuの専門家と最適なソリューションを見つけましょう!